
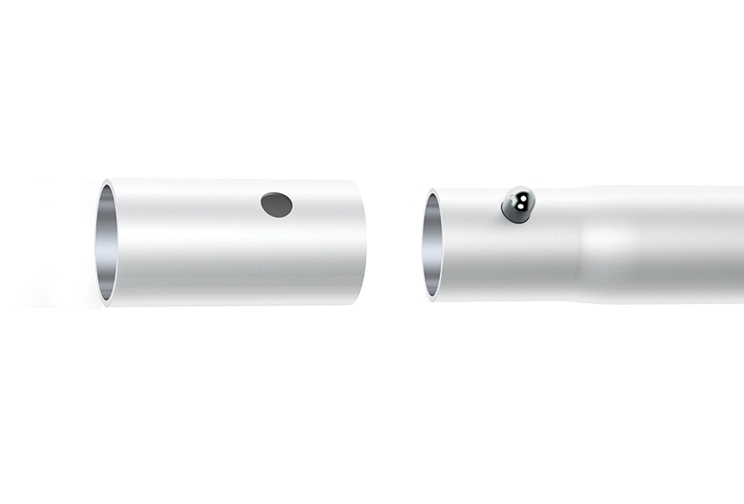
The most common use of swaging is to attach fittings to pipes or cables (also called wire ropes) the parts loosely fit together, and a mechanical or hydraulic tool compresses and deforms the fitting, creating a permanent joint. Heat swaging is a similar process to heat staking, but it involves rolling or reforming a wall (typically a perimeter) of a plastic part to retain another part or component. The swaging is an alternative or supplement to soldering.

Typical pin diameter range from 0.017 to 0.093 inches (0.43mm to 2.36mm) or larger. Some pins have a hollow end that is pressed over by the arbor's tool to form a mushroom-shaped retaining head. In printed circuit board assembly individual connector pins are sometimes pressed/swaged into place using an arbor press. Swages are used for shaping the metal in various ways, to enhance its beauty or its fit for a desired purpose. A butt swaging machine can allow a workpiece to be inserted without the dies closing on it, for example a three-foot (90 cm) workpiece can be inserted 12 inches (30 cm) and then the dies closed, drawn through until 12 inches (30 cm) remain and the dies are then released, the finished workpiece would then, for example, be four feet (120 cm) but still of its initial diameter for one foot (30 cm) at each end. A butt swaging machine works by having sets of wedges that close the dies onto the workpiece by inserting them between the annular rollers and the dies, normally by the use of a foot pedal. There are two basic types of rotary swaging machine, the standard (also known as a tagging machine), and the butt swaging machine. On a four-die machine, the number of rollers cause all dies to close at a time if the number of rollers do not cause all pairs of dies to close at the same time then the machine is called a rotary forging machine, even though it is still a swaging process.Ī variation of the rotary swager is the creeping spindle swaging machine where both the spindle and cage revolve in opposite directions, this prevents the production of fins between the dies where the material being swaged grows up the gap between the dies. The rollers are larger than the cage so as the spindle spins the dies are pushed out to ride on the cage by centrifugal force, as the dies cross over the rollers they push the dies together because of their larger size. The spindle is mounted inside a cage containing rollers (looks like a roller bearing). This action is achieved by mounting the dies into the machine's spindle which is rotated by a motor. Grease is often used to lubricate this swaging process, which is also called roller swaging.Ī swaging machine works by using two or four split dies which separate and close up to 2,000 times a minute. The flaring is done with a pair of rolls that travel around the hole and are fed down into the part, deforming the metal in a controlled, predicted way. Swaging a bearing into a housing means either flaring its groove's lips onto the chamfer of the housing, or flaring the housing's material over the edge of the bearing. It can also impart internal shapes in hollow workpieces through the use of a mandrel (the shape must have a constant cross-section). Rotary swaging is usually a cold working process, used to reduce the diameter, produce a taper, or add a point to a round workpiece. Swaging is normally the method of choice for precious metals since there is no loss of material in the process. Tubes may be tagged (reduced in diameter to enable the tube to be initially fed through the die to then be pulled from the other side) using a rotary swager, which allows them to be drawn on a draw bench. This process is usually called "rotary swaging" or "radial forging".
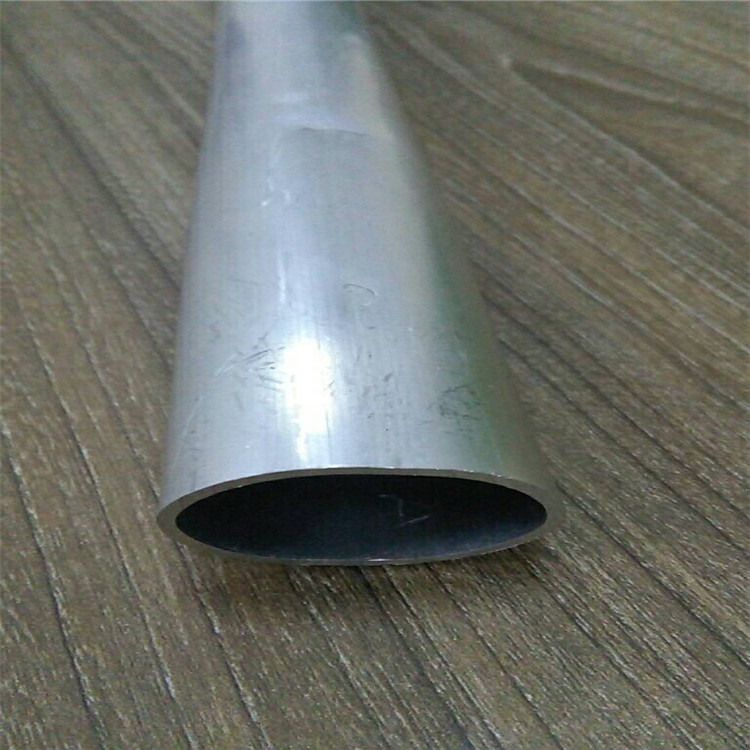
Swage blocks are anvil-like dies with various shapes forged into them, which are also used for forming metal. These have handles for holding or pegs for attaching to an anvil, and often a flat head for striking with a hammer. Swages were originally tools used by blacksmiths to form metal into various shapes too intricate to make with a hammer alone. The term "swage" comes from the Old French term souage, meaning "decorative groove" or "ornamental moulding".
